
Plus One Robotics does the heavy lifting
A huge variety of package shapes, sizes, weights and colors pass through today’s e-commerce fulfilment or warehouse distribution centers. Using sensors, cameras and data, the Plus One Robotics perception system provides the eye-hand coordination that enables a robot to see where to pick and place packages across a range of common warehouse applications including picking, order packing, depalletization and quality checking.
Why it’s important
The AI and depth powered computer vision software automates robots so that they can do the heavy lifting of dull, dirty and dangerous work that is not ergonomically friendly for the human body. With increased demand from consumers for rapid e-commerce delivery, combined with labor shortages, Plus One helps warehouse operators improve efficiency as well as workplace satisfaction and safety.
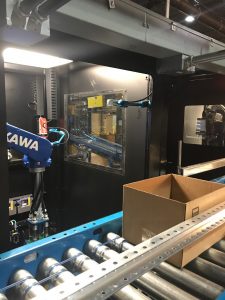
Plus One Robotics powers packaging and picking solutions
People and robots working together
Plus One robotics approaches human-robot collaboration in a way that ensure systems are flexible and fault-tolerant. Instead of performing the heavy physical labor, people are moved to value-add positions, including a Crew Chief role, where one person manages a team of robots. The solution allows one person to manage up to 50 robots, with the ability to see on screen what the robot sees. In situations where the robot gets confused by what it sees, such as shiny materials that can confuse sensors, it can raise its hand for help. The Crew Chief can see the problem on screen and help it resolve exceptions quickly. This approach to supervised autonomy allows for 24/7 service.
Efficient material handling and higher levels of throughput, where packages move quickly through an order fulfillment center, mean happier customers. Parcel orders can be inducted, sorted and packed for distribution, arriving on time to consumers. On-time delivery has never been more important, especially in sectors like food distribution or pharmaceuticals. Innovations in robotics automation can help these sectors grow without sacrificing efficiency or customer satisfaction.
How does it work?
Intel RealSense technology is used in many applications by Plus One robotics. For some customers, they have developed order packing solutions that can pack around 600 orders per day per robot. The robot takes the contents of an order tote and place it into a box that then gets shipped out to the customer. Using an Intel RealSense depth camera D415, the robot views the contents of the tote and also the contents of the box. As it performs the task, the robot can see the items in the order tote to either pick them up individually or together and place them in the box. It uses a second depth camera to inspect the box to make sure nothing is hanging out or overtopping the box. By using the depth cameras in this way, it can handle both performing the picking task, the order packing and also the quality checking component of the task, for excellent results regardless of the different items to be packed.
Plus One uses a dedicated camera for each action, one of the significant benefits of working with the D415. Other industrial cameras are less cost effective and slower. By using more than one D415, a dedicated camera can be used for each task, leading to a more flexible solution with wider fields of view and more mounting options. Using more than one camera also adds redundancy for problematic materials such as clear, shiny or matte black packaging materials. With more than one angle, the second camera can help resolve some issues with such packaging or help notify the Crew Chief sooner. They can then take over temporarily to guide the robot with the best pick or place point for the package.
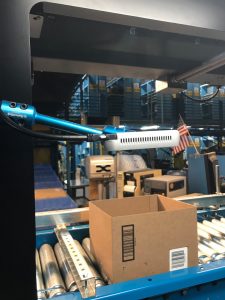
The Intel RealSense Depth Camera D415 scanning the contents of a box
Why depth and Intel RealSense Technology?
For PickOne, the 3D and AI-powered vision software used in these warehouse applications, depth is essential. A robot arm needs a certain amount of space to perform freely, so having depth perception helps it understand where to pick an item in a tote. Within the tote, depth is used to determine the next layer of pick points for the items it contains.
Working with Intel RealSense depth cameras enables Plus One to use affordable quality sensors in their logistics applications for customers. With different SKUs and package types in fulfilment or distribution centers, more sensors enable greater depth and field of view, giving more flexibility to handle any materials. High quality sensor capabilities at a lower cost means that Plus One can pass on efficiencies to customers, with more room in the budget for higher end processors. Better compute ultimately delivers greater efficiencies and throughput.
Check out the Plus One ebook for an example case study and more information.
Subscribe here to get blog and news updates.
You may also be interested in
In a three-dimensional world, we still spend much of our time creating and consuming two-dimensional content. Most of the screens
In this How-To, we are going to share a simple way to 3D scan an environment that you can then